Your Custom Lift and Work Platform Experts
With over 42 years of experience, LPI Lift Systems, located in Eau Claire, WI., has been designing and fabricating personnel lifts and work platforms that are purpose-built for specific applications. What sets us apart is the depth of our standard lift product line, plus our ability to work with our many customers to create custom solutions when they need equipment that is not off the shelf.
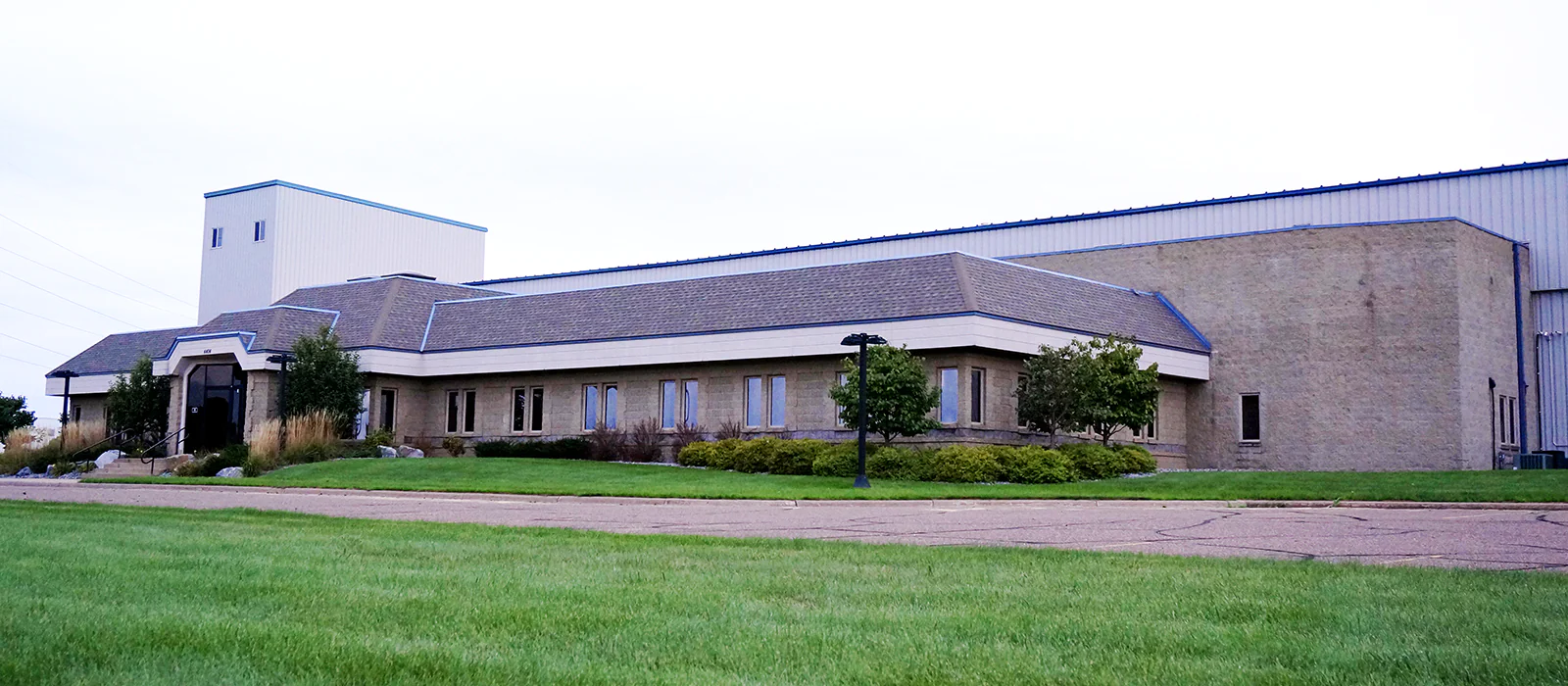
42+ Years
In Business
150+ Years
Engineering Experience
5,000+
Worldwide Customers
Our valued customers have trusted us repeatedly to deliver solutions for fall prevention and product access in various industries and industrial processes, from welding areas to inspection bays and every aspect of manufacturing in between. Our team understands industrial processes and will work with you throughout the process to provide the right cost-effective solution for your application.
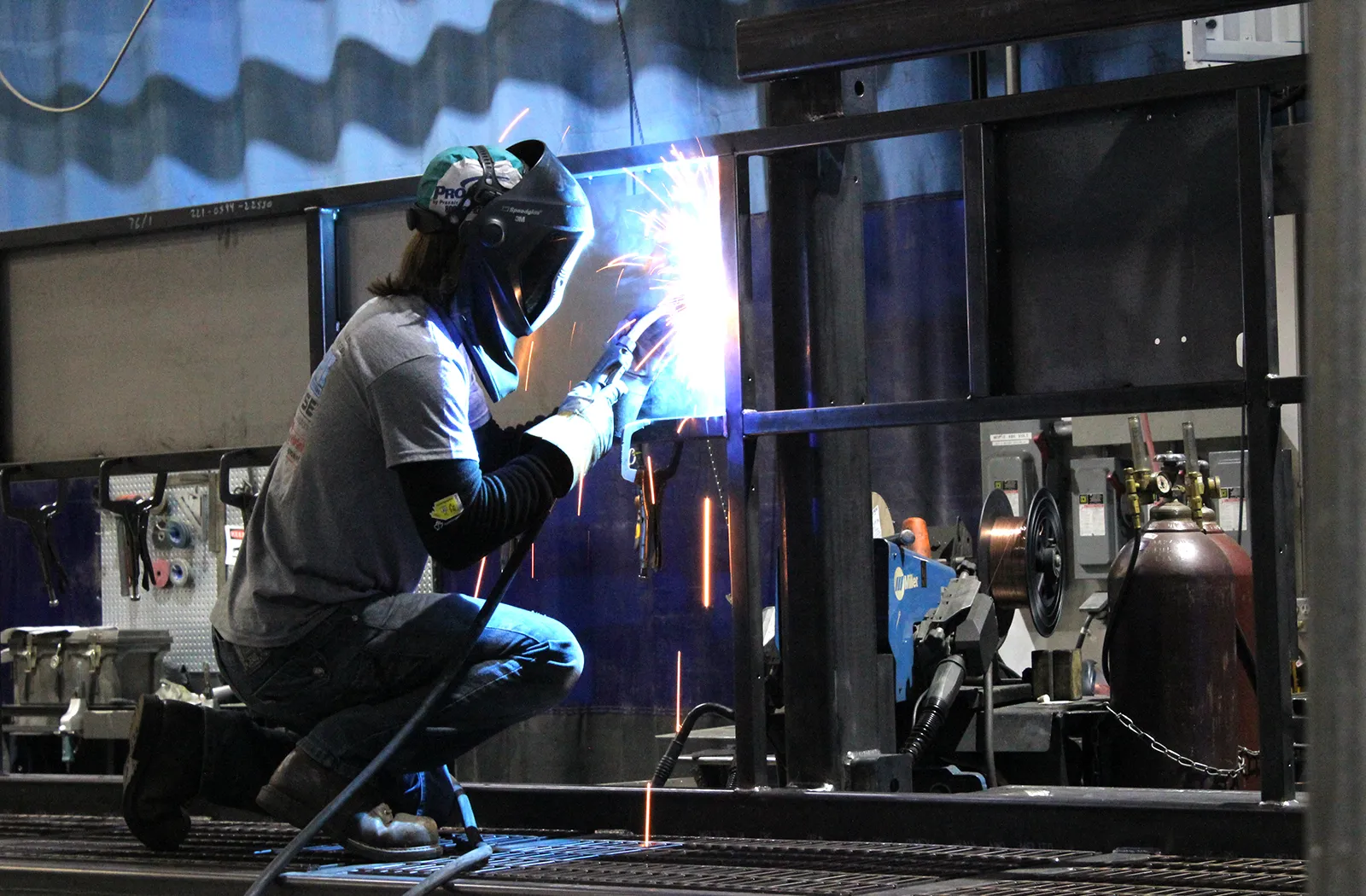
Quality products built by quality people go a long way
At LPI, our products are built utilizing high-quality components to provide reliability, dependability, and durability by a team that boasts over 150 years of combined engineering experience in the lift platform industry.
Our team is comprised of problem solvers from the shop floor to the sales floor. Many of our lift systems built over 30 years ago are still in use today. We make products built to last and solutions as custom as your business.
Get the job done right with LPI
We know what it takes to get the job done and get it done right – right on time and right on budget. That’s why the team at LPI considers mechanical design, ergonomics, safety, maintenance, and optimization of process to address present requirements and anticipates changes in the future. Through the use of a project interview process, we collect and exchange information about your work process and challenges and any need for integrated equipment. This allows us to create a solution-based design that addresses your needs while considering your budget.
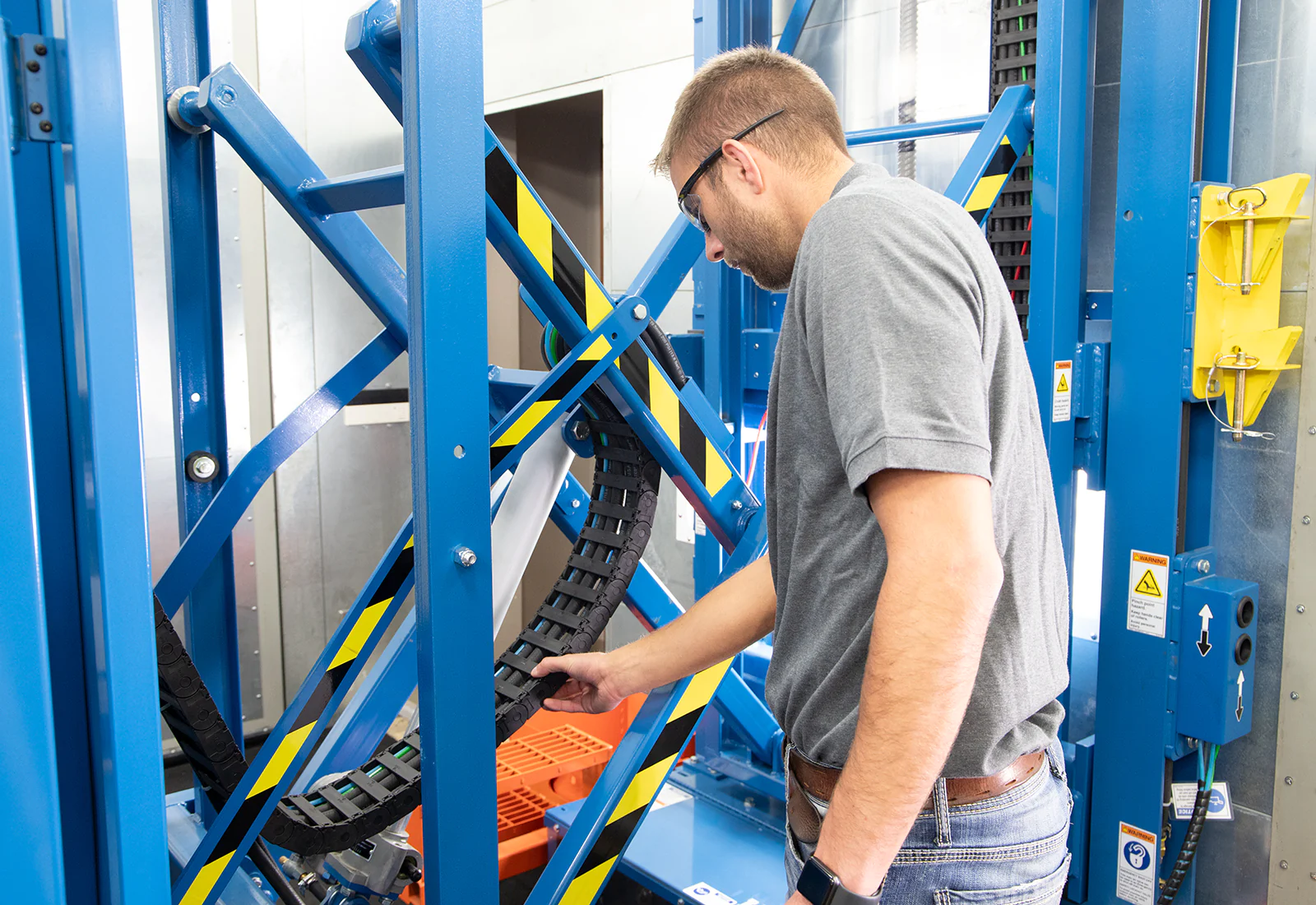